Robotic grinding of welded parts
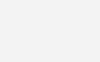
Grinding of welded parts
The grinding of welded parts is a special process. It depends on many parameters and predetermines the quality and outlook of the final products – i.e. details with visible welding, sheet metal boxes and chassis, structures of welded profiles, etc. Manual grinding requires skill, good control and high precision. In addition, the process predetermines polluted environment.
There is a set of factors that directly affect the quality obtained in manual grinding:
- The quality of the abrasive material.
- The pressure on the product by grinding.
- The grinding time.
- The angle of the grinding material/tooling to the workpiece.
- The speed of movement of the grinding material.
- Compensation for the deviations of the product.
Robotic grinding of welded parts
The grinding process of welded parts can be robotized. The following problems are solved:
- Sustainability and consistent quality even when working 24/7
- Increased productivity by lack of personnel for processes in an unfavorable working environment.
- Optimization of the processing cycle and reduction of time.
- Cost reduction by minimizing abrasive consumption – grinding exactly where it needed and just as much as it needed.
- Abrasive materials can be used longer.
- Improved working environment and employee satisfaction.
In general, robotic grinding solutions are such in which the product is fed to the grinding unit or such where the robot “holds” and feeds the grinding aggregate to the product. The solution is strictly individual, but most often it depends on the dimensions and weight of the parts, as well as the required grinding aggregate and finish.
Challenges in a robotic grinding solution are:
- Tolerance deviation of the welded parts. It is highly recommended to robotically grind parts that are prior welded by robot and with the smallest possible deviations.
- Parametric definition of time, pressure and speed, depending on the abrasive wear rate and the desired result.
- Positioning and feed angle of the workpiece.
- Design of a suitable gripper and positioners for each specific detail.
- programming of the robotic system for each specific detail.
The solution for robotic grinding in DeBulCo Ltd.
A main goal of DeBulCo is to seek and offer its customers the most appropriate and advanced technologies in production. This allows us to offer excellent quality, attractive prices, and very short delivery terms. After the integration of welding robotic cells, а logical extension in our production process was an investment in a grinding robot cell.
A universal solution with a Fanuc robot with a load capacity of 170 kg and a two-belt grinding unit was chosen. The robotic system allows grinding of parts with a complex shape up to 3000 mm. The two belts allow achieving of two different finishes in one cycle – rough and fine grinding of a workpiece. The concept allows continuous operation – taking of workpiece by the robot, processing, leaving, picking up the next workpiece, etc.
The results of the integration are increased productivity, consistency and improved product quality, cost reduction, a better working environment, fast delivery times and satisfied customers.
If you need more information about our services, please contact us : info@debulco.bg or call us: +359888703887.