Precision and productivity with DeBulCo’s new turning center
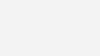
The new turning center
The new DMG MORI CLX 350V6 universal turning center is the latest generation of the German manufacturer’s CLX series metal-cutting machine. The machine allows turning of details of up to D320 mm in diameter. The maximum axis stroke is X=185 mm, Y=80 mm, Z=540 mm. The maximum workpiece length is 530 mm. The compact design in combination with the large operation area allows the machining of specific parts. The machine has a 45° inclined bed for smooth removal of chips from the work area. Materials up to D65 mm are fed and processed automatically using the installed bar feeder. The DMG MORI CLX 350V6 is equipped with a high-tech 3D control system with a touch control panel, a direct measurement system, a 12-stations VDI turret, and more.
The lathe is equipped with 2 spindles and a milling Y axis for more complex and productive processing of parts. The highly dynamic main spindle is driven at a maximum speed of up to 5000 revolutions per minute. The sub spindle as integrated motor spindle ISM 36 and max. speed up to 5.000 rpm enables rear-face machining. The milling Y axis has a stroke range of ±40 mm and allows complete processing of side surfaces.
The machine features integrated IoTconnector technology for digitized and connected production processes. It is equipped with intelligent digital solutions NETservice – direct remote connection to DMG MORI Service, Messenger – real-time monitoring of connected machines and devices, an integrated security network with automatic updates.
Advantages
Compactness and functionality
Since the machine has a compact design and is equipped with two spindles, this leads to greater efficiency – it provides two-side complete machining of parts with one program and without interception. Moreover, the dual spindle configuration of the CLX 350V6 extends its service life because the load and wear is distributed between the two spindles.
Accuracy of processing
The dual spindle configuration of the machine will achieve a high level of precision of processing. With a speed of 5,000 rpm, the highly dynamic spindle can process complex, high-quality components and ensure precision and accuracy of the parts. The additional spindle unit provides the possibility for rear-face machining, the Y-axis allows for more efficient lateral surface machining. This achieves six-sided complete machining of complex turned parts.
Quality machining of the components
An additional advantage of dual spindle machining on the same lathe is the consistent quality of the products, as there is no need to move to different workstations. The parts are processed using state-of-the-art technologies and software solutions which boasts not only speed and precision but also high quality of the components. The process is strictly managed and controlled by the installed digital solutions.
High performance and productivity of production
DeBulCo’s investment in the CLX 350V6 dual spindle lathe will contribute to better efficiency and performance in machining metal products both for its own needs and for external customers.
Cost savings and economy of resources
The integration of more functions, tools and machining operations in the same machine allows for economical production of items in small batches. This reduces the manufacturing costs per product unit which affects its price and makes it competitive in the market. Technological integration saves resources and decreases CO2 emissions, while digitalization reduces energy consumption. Thus, some of the positive effects of introducing the new turning center in machining are the more efficient use of resources and the optimization of operating costs. And this, in turn, makes production economical and sustainable.
If you want to learn more about DeBulCo services, contact us by sending an email to info@debulco.bg or calling 0888 703887.